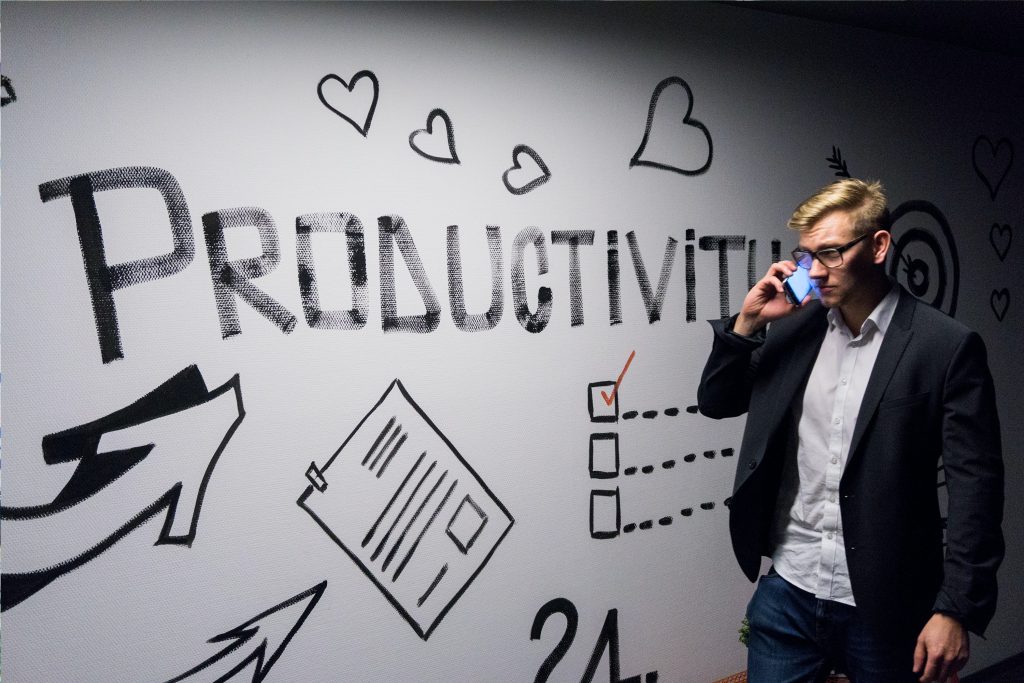
La méthode Kaisen repose sur une constatation : les grandes transformations sont plus difficiles à mettre en place et à faire accepter qu’une série de petits changements. Cette méthode est née dans les années 50 au Japon et fut d‘abord appliquée dans les usines Toyota, dans le cadre de la mise en place du « Toyota Production System », devenu par la suite le lean management. L’objectif de la méthode Kaisen est d’améliorer la productivité des salariés et de l’entreprise, par le biais d’évolutions et de corrections constantes. Les principaux axes d’améliorations sont la minimisation des risques, la chasse au gâchis et l’ergonomie des postes de travail.
La méthode Kaisen : un état d’esprit
La méthode Kaisen est davantage un état d’esprit qu’une méthode. À ce titre, elle repose sur plusieurs principes :
- L’anticipation : prévoir les problèmes éventuels pour les résoudre avant qu’ils n’apparaissent ;
- L’amélioration continue : toujours s’interroger sur la possibilité d’améliorer les procédures de fabrication ;
- L’empowerment : impliquer les collaborateurs dans la résolution des problématiques ;
- La prise collective de décisions : mettre les idées en commun permet d’opposer les avis et de tenir compte de plusieurs points de vue ;
- La causalité : application de la méthode des 5 pourquoi pour agir à la source du problème ;
- La quête de l’économie : les petites améliorations sont moins coûteuses que les grands bouleversements, c’est pourquoi la méthode Kaisen prône les petits “réglages” plutôt que les métamorphoses.
Avantages de la méthode Kaisen
La méthode Kaisen correctement appliquée mène à des résultats rapidement visibles :
- La satisfaction des collaborateurs : ils sont plus impliqués dans la vie de l’entreprise grâce à la prise en compte de leur avis et de leurs conditions de travail ;
- L’amélioration du travail d’équipe : les collaborateurs satisfaits et appelés à prendre des décisions collectivement communiquent mieux, et les informations circulent mieux ;
- La satisfaction des clients : l’amélioration de la qualité des produits facilite également leur fidélisation ;
- Le gain de rapidité et d’efficacité : grâce à l’optimisation continue des tâches ;
- La réduction des délais : grâce à une organisation plus performante ;
L’ensemble de ces progrès mène à une amélioration de la productivité et des performances de l’entreprise.
Méthode Kaisen : les outils
L’application de la méthode Kaisen repose sur l’utilisation de 4 outils : les 5 S, les 3 M, les 5 “pourquoi” et le PDCA.
Les 5 S de la méthode Kaisen
Ces 5 S sont relatifs à l’organisation de l’espace de travail et font référence à 5 mots japonais :
- Seiri : Débarrasser, optimiser l’espace de travail en ôtant tout ce qui est inutile ;
- Seiton : Ranger pour retrouver facilement les dossiers importants ;
- Seiso : Nettoyer pour travailler sur un espace propre ;
- Seiketsu : Maintenir l’ordre en gardant l’espace de travail rangé ;
- Shitsuke : Être rigoureux et respecter les 4 règles précédentes.
Les 3M de la méthode Kaisen
Cet outil vise à repérer et à éliminer les 3 sources de gaspillage récurrent dans une entreprise :
Muda : désigne une activité improductive. On en dénombre en principe 7 :
- le stock dormant ;
- la surproduction ;
- les temps d’attentes trop longs ;
- les déplacements inutiles ;
- les transports inutiles ;
- les opérations de traitement inutiles ;
- le défaut qualité qui nécessite souvent une tâche supplémentaire de correction.
Mura : désigne la survenue d’irrégularités dans l’accomplissement d’un processus entraînant par exemple une baisse de production.
Muri : désigne la survenue brutale de difficultés à accomplir une tâche. Ces difficultés proviennent directement des deux premiers M : mida ou mura, ou peuvent être causées par d’autres facteurs, comme un manque de compétence, d’expérience, de formation ou encore de matériel adapté.
L’analyse de ces 3 M permet d’identifier les sources de gaspillage, de façon à pouvoir les faire disparaître et ainsi gagner en productivité.
Les 5 « Pourquoi » de la méthode Kaisen
La méthode Kaisen tend à parvenir à une efficacité optimale en procédant à l’amélioration continue des processus de fabrication et des conditions de travail. Pour y parvenir, il est nécessaire d’identifier l’origine des problèmes ou dysfonctionnements. L’utilisation des 5 « pourquoi » permet de remonter question après question, ou plutôt réponse après réponse, à la racine du problème, pour pouvoir l’éradiquer à la base. Cet outil permet également de résoudre un problème sur la durée plutôt que de façon ponctuelle.
Par exemple : une machine tombe en panne régulièrement.
« Pourquoi ? » Parce qu’elle s’encrasse.
« Pourquoi ? » Parce que son entretien n’est jamais fait à temps.
« Pourquoi ? »Parce que l’entreprise chargée de cet entretien met du temps à intervenir quand on l’appelle.
« Pourquoi ? » Parce qu’on l’appelle toujours en urgence.
« Pourquoi ? » Parce que personne n’est chargé de suivre l’entretien de cette machine.
Solution : nommer quelqu’un qui sera chargé de prévoir avec le prestataire l’entretien du dispositif, de façon à programmer l’intervention avant qu’elle ne soit urgente. Ainsi la machine sera entretenue plus régulièrement et ne tombera plus en panne.
Le PDCA
Le PDCA, appelé aussi roue de Deming, désigne les 4 étapes à suivre pour améliorer la qualité d’une organisation :
1/Plan : Planifier ;
2/Do : Faire ;
3/Check : Vérifier ;
4/Act : Ajuster.
Cet outil se représente sous la forme d’une boucle fermée, comme un cercle vertueux. Il s’applique dans de nombreuses situations dans le cadre du principe de base de la méthode Kaisen, l’amélioration continue.
En conclusion, la méthode Kaisen se définit comme radicalement opposée au reengineering, qui déstructure une organisation pour mieux la reconstruire. Cette méthode tend à démontrer qu’une succession de petits pas peut mener à de grandes réalisations. Utilisée dans l’industrie, la méthode Kaisen est applicable dans tous les domaines, y compris la sphère privée.